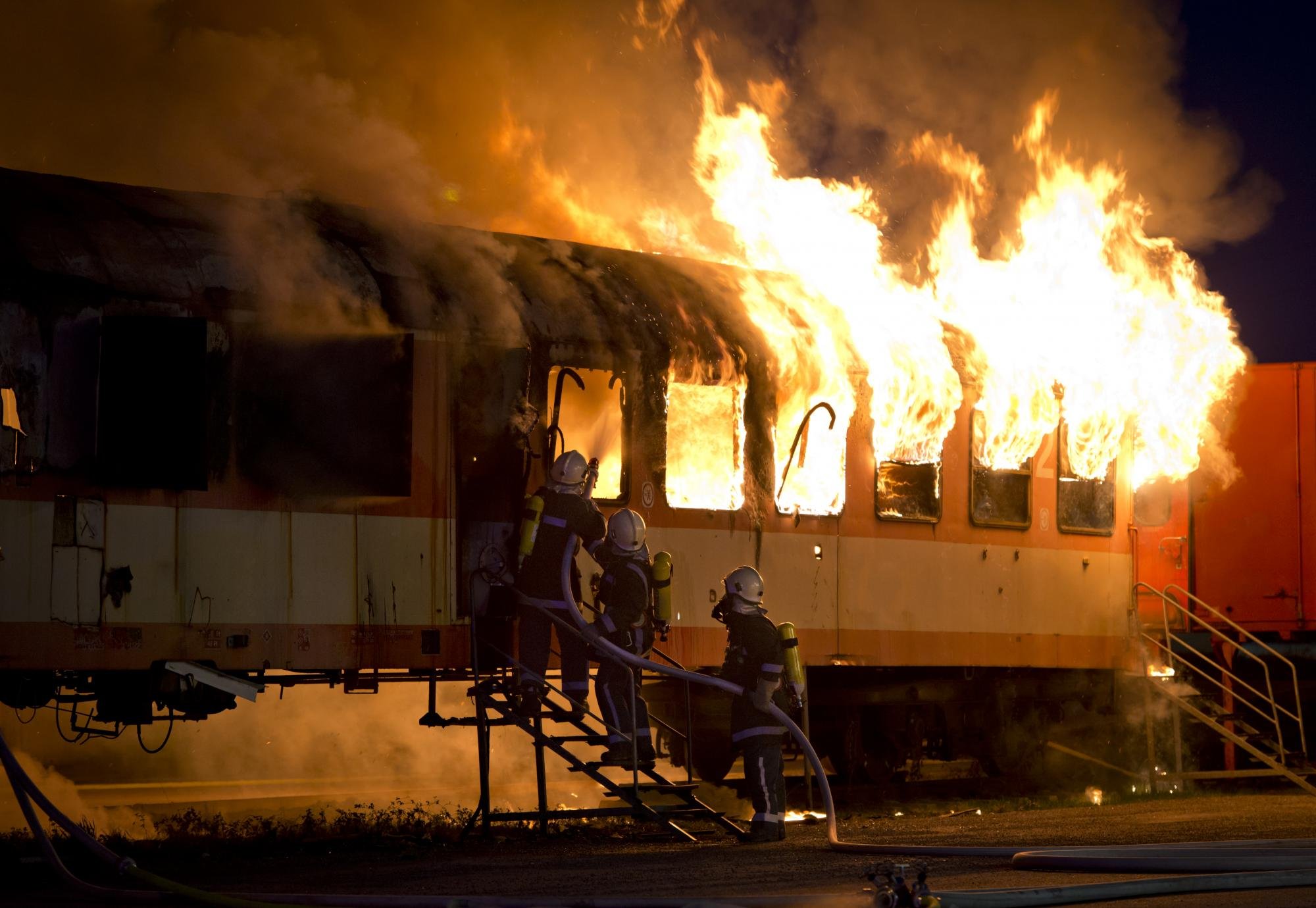
EN 45545-2 Fire Test Methods and Classification for European Railway Materials
What is the EN 45545?
EN 45545 is the mandatory European standard for materials used in the manufacture of rail vehicles. It aims to protect passengers and staff from fire on board railway vehicles.
EN 45545 was published in 2013, and became a mandatory requirement throughout Europe in 2016. All materials used in the manufacture of railway vehicles must follow the EN45545 standard to achieve the highest possible level of safety in case of fire. It applies to rail vehicles, including high-speed trains, regional trains, streetcars, subways and double-decker trains.
The standard series EN 45545 contains the following parts:
Part 1: General
Part 2: Requirements for fire behaviour of materials and components
Part 3: Fire resistance requirements for fire barriers
Part 4: Fire safety requirements for rolling stock design
Part 5: Fire safety requirements for electrical equipment
Part 6: Fire control and management systems
Part 7: Fire safety requirements for flammable liquid and flammable gas installations
How EN 45545 Created?
With the creation of the European Union, the process of economic integration is increasing, and the European railway network is integrated. However, each EU country and region has its own railway fire safety standards, adopting test methods, and technical requirements that are not analogous to each other, each country is interested in protecting its domestic standards system and industrial system, and national railway companies are responsible for their own operational and technical requirements development and certification; then there is a strong demand for integration from operators and suppliers.
The European Commission issued Directive 2008/57/EC in 2018 on the interoperability of railway systems within the European Community. The new Directive replaces 96/48/EC, and 2001/16/EC.
It requires the integration of railway systems within the EU. EN 45545 takes benefits including, replaced different national fire protection standards, enhanced European railway fire safety, increased European network interconnection, and reduced duplication of development and testing costs.
EN 45545 became the unique rail fire protection standard in March 2016, and replaced the following national standards:
England BS 6853 Code of practice for fire precautions in the design and construction of passenger carrying trains
France NF F 16-101 Railway Rolling Stock Fire Behavior Choice of Material
Germany DIN 5510-2 Preventive Fire Protection In Railway Vehicles - Part 2: Fire Behaviour And Fire Side Effects Of Materials And Parts - Classification, Requirements And Test Methods
Itlay UNI CEI 11170-1/2/3 Railway and Tramway Vehicles - Guidelines for Fire Protection of Railway, Tramway and Guided Path Vehicles
Poland PN K-02511 Rolling Stock - Fire Safety of Materials - Requirements
EN 45545 Purpose
The purpose of the EN 45545 series of standards is to protect passengers and staff by minimizing the possibility of fire and controlling the speed and extent of its development once it has occurred.
The protection of passengers and staff is essentially based on the following measures.
Measures | EN 45545 |
---|---|
Prevents fires caused by technical defects, equipment design defects, and vehicle design defects. | Part 1, 4, 5, 7 |
Minimizes the possibility of the materials fitted to the vehicle igniting in the event of an accident or vandalism. | Part 1, 2 |
Fire detection | Part 6 |
Limits the spread of fire | Part 2, 3 |
Minimizes the impact on passengers and staff in terms of heat, smoke, and toxic gases from fire. | Part 2 |
Control and management of fires. | Part 6 |
EN 45545 Categories
EN 45545 classifies railway vehicles according to the range of railway vehicle types, operation, and infrastructure characteristics.
Operation Category depends on the type of service operated and the infrastructure characteristics.
Operation Category | Description | Running Time | Minimum Average Speed |
---|---|---|---|
OC1 | Vehicles for operation on infrastructure where railway vehicles may be stopped with minimum delay, and where a safe area can always be reached immediately. | Vehicles may stop with minimum delay | Not Applicable |
OC2 | Vehicles for operation on underground sections, tunnels and/or elevated structures, with side evacuation available and where there are stations or rescue stations that offer a place of safety to passengers, reachable within a short running time. | 4 min | 80 km/h |
OC3 | Vehicles for operation on underground sections, tunnels and/or elevated structures, with side evacuation available and where there are stations or rescue stations that offer a place of safety to passengers, reachable within a long running time. | 15 min | 80 km/h |
OC4 | Vehicles for operation on underground sections, tunnels and/or elevated structures, without side evacuation available and where there are stations or rescue stations that offer a place of safety to passengers, reachable within a short running time. | 4 min | No requirement |
Design Category depends on characteristics of the vehicle design and layout.
Operation Category |
---|
A: Vehicles forming part of an automatic train having no emergency trained staff on board; D: Double decked vehicles; S: Sleeping and couchette vehicles; N: All other vehicles (standard vehicles) |
The Operation Category combined with the Design Category gives the hazard level (HL1, HL2, HL3) which determines which of the material testing requirements set out in EN 45545-2 are applicable.
EN 45545-2 Test Methods
EN 45545-2 specifies the reaction to fire performance requirements for materials and products used on railway vehicles as defined in EN 45545-1.
The operation and design categories defined in EN 45545-1 are used to establish hazard levels that are used as the basis of a classification system. For each hazard level, this part specifies the test methods, test conditions and reaction to fire performance requirements.
Material Groups
Depending on the usages & characteristics of the materials and components, EN 45545-2 specifies materials into interiors products (IN), exteriors products (EX), Furniture (F), electro technical equipment (E), mechanical equipment(M), and non-listed products.
Test Requirements
Each of these product groups are required to meet a specific set of performance requirement levels ( R1 to R28).
Test Methods
EN 45545-2 specifies 27 test methods (T01 to T17).
The performance of all the products is determined with respect to ignitability, flame spread, heat release, smoke release, and toxic gases produced. Each requirement has a corresponding series of test performance criteria imposed for each fire risk level (HL 1 to HL 3).
Lastly, the material will be ranked as RxHLy based on the test requirements, test methods.
EN 45545-2 Ranking Schematic
EN 45545-2 Requirement Sets & Test Methods
T01 Oxygen Index
Oxygen Index Tester
Compliance: EN ISO 4589-2
Summary:
Determines the minimum concentration of oxygen percentage that just support the material flaming under a constant airflow and ambient temperature.
A small test specimen is supported vertically in a mixture of oxygen and nitrogen flowing upwards through a transparent chimney. The upper end of the specimen is ignited and the subsequent burning behavior of the specimen is observed to compare the period for which burning continues, or the length of specimen burnt, with specified limits for each burning. By testing a series of specimens in different oxygen concentrations, the minimum oxygen concentration is determined by the particular calculation.
Test Criteria:
The minimum oxygen index, OI, in %.
MOTIS’s Oxygen Index Tester:
Compact benched mounted design, easy-to-use.
Precise paramagnetic oxygen transducer.
Precise mass flow meter.
Portable flame igniter.
Multiple specimen holders with fixture tools.
T02 Lateral Flame Spread
LIFT, IMO Spread of Flame Apparatus
Compliance: EN ISO 5658-2
Summary:
Measures the lateral spread of flame along the surface of a specimen of a product mounted in a vertical position under a specific gas-fired radiant heat panel.
A test specimen is placed in a vertical position adjacent to a gas-fired radiant panel where it is exposed to a defined field of radiant heat flux. A pilot flame is sited close to the hotter end of the specimen to ignite volatile gases issuing from the surface. Records the flame front spread distance horizontally along the length of the specimen and the time it takes to travel various distances.
Test Criteria:
The minimum critical flux at extinguishment, CFE, in kW/m2.
MOTIS’s LIFT, IMO Spread of Flame Apparatus:
Steady framework for the radiant panel, and specimen holder support.
Porous ceramic refractory radiant panel.
Precise mass flow meter for radiant panel flue supply.
Maintenance-free air supply system to radiant panel.
Precise Schmidt-Boelter heat flux meter, with water cooling device.
15” Touch screen operation.
T03 Heat Release Rate
Cone Calorimeter
Compliance: EN ISO 5660-1
Summary:
Measures the heat release rate and dynamic smoke production rate of specimens exposed in the horizontal orientation to controlled levels of irradiance with an external igniter. The heat release is calculated according to the oxygen consumption principle.
A test specimen is supported horizontally under a conical heater, specimen in the test is burned under ambient air conditions while being subjected to a 25 or 50 kW/m2 irradiance. The combustion gases are collected and analyzed to calculate the heat release, smoke release…
Test Criteria:
The maximum average rate of heat emission, MARHE, in kW/m2.
MOTIS’s Cone Calorimeter:
Compact floor mounted instrument body, flexible layout placement.
Full function oxygen consumption principle heat release calorimetry.
Equip with Paramagnetic type O2 analyzer, & NDIR type CO/CO2 analyzer.
Precise mass flow controller for calorimeter self-calibration.
Smart Cone software, function includes, sensor monitor, sensor calibration, system self-calibration, standard test procedure, and report management.
T04 Horizontal Flame Spread of Floorings
Flooring Radiant Panel
Compliance: EN ISO 9239-1
Summary:
Measures the critical radiant flux of horizontally-mounted floor covering systems, which are exposed to a flaming ignition source in a specific radiant heat environment.
The test specimen is placed in a horizontal position below a gas-flued radiant panel inclined at 30° where it is exposed to a defined heat flux. A pilot flame is applied to the hotter end of the specimen. During the test, any flame front which develops is noted and a record is made of the progression of the flame front horizontally along the length of the specimen in terms of the time it takes to spread to defined distances, which is reported as critical radiant flux, in kW/m2. Also, the smoke development during the test is recorded as the light transmission in the exhaust stack.
Test Criteria:
The minimum critical heat flux at extinguishment, CHF, in kW/m2.
MOTIS’s Flooring Radiant Panel:
Integrated instrument body.
Porous ceramic refractory radiant panel.
Precise mass flow meter for radiant panel flue supply.
Maintenance-free air supply system to radiant panel.
Precise Schmidt-Boelter heat flux meter, with water cooling device.
Fast heat flex meter positioning device for calibration.
15” Touch screen operation.
Easy to use operation software, comforts to ISO 9239-1, ASTM E648, etc.
T05 Single-Flame Source Test
Ignitability Apparatus
Compliance: EN ISO 11925-2
Summary:
Determines the ignitability of material by direct small flame impingement to vertically mounted specimens without additional irradiance.
A specimen is mounted vertically and exposed to a small flame (20mm height) for 30 seconds. The flaming time (after the small flame removal), flame spread height, and presence of droplet/particles is recorded during the test.
Test Criteria:
The flame spread distance in the 60s, in mm.
MOTIS’s Ignitability Apparatus:
Full stainless steel made for long use life.
Sliding flame burner carriage.
Precise gas valve for propane flame control.
Easy to use.
T06 Calorimeter for vandalized and unvandalized seats
EN 16969 Calorimeter for Railway Seat
Compliance: EN 16989
Summary:
Measures the heat release rate of a complete seat which is exposed to a defined propane flame.
The test seats are subjected to a 15kw propane-flued ignition source under an exhaust hood with a well-ventilated condition. The measurement to be made include the heat release rate (HRR), maximum average heat release (MARHE), total smoke production (TSP), and flame height.
Test Criteria:
The maximum average rate of heat emission, MARHE, in kW/m2.
MOTIS’s EN 16989 Calorimeter:
Complete test system for EN 16989
Stainless steel hood and ducts for long life use.
Stainless steel burner carriage, with application force load adjustment.
Precise mass flow controller for 15kW propane flame and system self-calibration.
Full function software, function includes sensor monitor, sensor calibration, system self-calibration, automatic standard test procedure, and report management.
T07 Ignitability of Bedding Items
Match-Flame Device
Compliance: EN ISO 11952-2
Summary:
Determine the ignitability of bedding items when subjected to a match-flame equivalent.
A test specimen is placed on a testing substrate, and subjected to a small open flame on the top and/or below the test specimen. The progressive smouldering ignition and/or flaming ignition is recorded.
Test Criteria:
Afterburn time, in second.
MOTIS’s Match-Flame Device:
Compact device, easy to place on any workbench.
Standard burner tube with silicon soft tube.
Butane MFC to provide a match-flame equivalent flame source.
Digital butane flow display.
Easy to operate.
T08 Flash and Fire Points
Cleveland Open Cup Flash Point Tester
Compliance: EN EN 60695-1-40, ISO 2592
Summary:
determination of flash and fire points of petroleum products using the Cleveland open cup method. It is applicable to petroleum products having open cup flash points between 79 °C and 400 °C.
The test specimen is filled to a specified level in the test cup. The temperature of the test cup will be increased rapidly (5 °C/min to 17 °C/min) at first and then at a slow constant rate (5 °C/min to 6 °C/min) as the flash point is approached. At specified temperature intervals, a small test flame is passed across the test cup. The lowest temperature at which application of the test flame causes the vapour above the surface of the liquid to ignite is taken as the flash point at ambient barometric pressure. To determine the fire point, the test is continued until the application of the test flame causes the vapour above the test portion to ignite and burn for at least 5 s. The flash point and fire point obtained at ambient barometric pressure are corrected to standard atmospheric pressure using a formula.
Test Criteria:
Fire point, in °C.
MOTIS’s Ceveland Open Cup Flash Point Tester:
Automatic test program, and export the test results.
7’’ Touch screen operation, easy to use.
Measuring range up to 400°C.
Precise temperature measurement, with a resolution of 0.1°C.
T09.01 Vertical Flame Propagation for a Single Insulated Wire & Cable
Flame Propagation Tester for a Single Insulated Cables
Compliance: EN 60332-1-2
Summary:
Determine the fire resistance to vertical flame propagation for a single vertical electrical insulated conductor or cable, or optical fibre cable, which is exposed to a 1 kW pre-mix flame.
A test specimen is mounted in a vertical position and is exposed to a 1 kW pre-mix flame for 60/120/240/480 seconds according to its diameter. The length of the charred zone is measured to evaluate its performance.
Test Criteria:
Charred zone length, in mm.
MOTIS’s Flame Propagation Tester:
Stainless steel test chamber with interior anti-corrosion coating for long life use.
Individual propane gas flow control and air flow control.
Sliding 1 kW air-gas pre-mixed burner.
Flame calibration kits, comply with IEC 60695-11-2.
Automatic flame application timer, four modes (60/120/240/480s) for rapid exchange.
T09.02, 09.03, 09.04 Vertical Flame Spread of Bunched Wires & Cables
Burning Behavirour of Bunched Cables
Compliance: EN 60332-3-24, EN 50305
Summary:
Assess vertical flame spread of vertically mounted bunched wires or cables, electrical or optical, under defined conditions.
Bunched cables or wires are mounted in a vertical position and exposed to a defined pre-mixed flame for 20mins. The length of the charred zone is measured to evaluate burning behavirour.
Test Criteria:
Charred zone length, in m.
MOTIS’s Burning Behavirour of Bunched Cables:
Stainless steel made test chamber with inner 65mm of mineral wool for thermal insulation.
High-temperature-resist observation window on the front.
AGF ribbon-type propane gas burner, with venturi mixer.
Individual propane gas flow control and air flow control.
Max. up to 2 AGF burner work at a time.
T10 Smoke Density Test
NBS Smoke Density Chamber
Compliance: EN ISO 5659-2
Summary:
Measures the specific optical density of smoke generated by the materials using a flat specimen (up to 25 mm thick) exposed to a specific radiant heat source (normally 25 or 50 kW/m2), in a closed chamber with or without a pilot flame.
A test specimen is placed in horizontal position under a conical heater which can output a radiant heat up to 50 kW/m2. The pilot burner flame is applied/non-applied upon the specimen. The generated smoke is collected in a closed chamber, which has a photometric system internal. The attenuation of a light beam passing through the smoke is measured. And the specific optical density is calculated accordingly.
Smoke Density Test Mode in EN 45545-2:
Heat flux 25 kW/m2, with pilot flame.
Heat flux 50 kW/m2, without pilot flame.
Test Criteria:
The Maximum optical density in the test chamber in the first 4 min, Ds(4).
The cumulative value of specific optical densities in the first 4 min of the test, VOF4.
The maximum optical density in the 10min test.
MOTIS’s NBS Smoke Density Chamber:
Integrated instrument body, which contains test chamber, photometric system, control unit, and touch screen computer.
Teflon coating on the internal chamber wall, provides a long use life.
Multiple test modes, comfort to the horizontal conical heater (ISO 5659-2) and the vertical heat furnace (ASTM E662).
Fast exchange between ISO 5659-2 and ASTM E662.
Multiple use operation software.
T11 FTIR Gas Analysis
FTIR Toxicity Gas Analysis
Compliance: EN 17084 Method 1
Summary:
Measures the toxicity gases generated during the smoke density test using the FTIR method, analyzed gases content including CO2, CO, HCl, HBr, HCN, HF, SO2, NOx.
Sample the combustion gas to FTIR spectrometer at 4min and 8min to analyse the toxicity gases content. Conventional index of toxicity (CITg) at 4min and 8min will be calculated to evaluate the performance.
Toxicity Test Mode in EN 45545-2 using NBS Smoke Density Chamber:
Heat flux 25 kW/m2, with pilot flame.
Heat flux 50 kW/m2, without pilot flame.
Test Criteria:
Conventional index of toxicity (CITg) at 4min and 8min.
MOTIS’s FTIR Toxicity Gas Analysis:
Quick connect to the NBS Chamber.
Heated filter up to 200°C.
Full heated tubes and connectors, temperature up to 200°C.
FTIR Spectrometer, MCT type detector, silicon carbide IR source, with a minimum resolution of 0.5 cm-1 and a path length of at least 2 m.
Operation software, associated with NBS Chamber, automatic sampling, continuous analysis, and calculation results.
T12 Toxicity Gas Analysis for Non-Listed Products
EN 17084 Method 2 Toxicity Gas Analysis
Compliance: EN 17084 Method 2, NF X 70-100-1, NF x 70-100-2
Summary:
Measures the toxicity gases generated from 1 gram material combustion in 600°C tube furnace, analyzed gases content including CO2, CO, HCl, HBr, HCN, HF, SO2, NOx.
Analysis Methods:
CO2 - NDIR CO2 Analyzer.
CO - NDIR CO Analyzer.
HCl - Ion Chromatography.
HBr - Ion chromatography.
HCN - Spectrophotometry.
HF - Ion Chromatography.
SO2 - Ion chromatography.
NOx - Chemiluminescence.
The conventional index of toxicity (CITnlp) will be calculated to evaluate the performance.
Test Criteria:
The conventional index of toxicity, CITnlp.
Instruments involved:
Tube Furnace & Sampling Device.
NDIR Type CO/CO2 Analyzer.
Ion Chromatography, for HCl, HBr, HF, SO2.
Spectrophotometry, for HCN.
Chemiluminescence Analyzer, for NO, NOx.
T13 Smoke Density Test for Cables
Compliance: EN 50305
Summary:
Measures the smoke emission when electric or optical fibre cables are burnt under alcohol flame source in a 3 metre cube chamber.
A test specimen is placed in a horizontal position upon a metal tray with 1 liter of alcohol inside. The specimen was burnt and the generated smoke is collected in a closed 3 metre cube chamber, which has a photometric system internal. The attenuation of a light beam passing through the smoke is measured.
Test Criteria:
Minimum Transmission, in %.
MOTIS’s 3 Metre Cube Smoke Density Apparatus:
3 Metre cube test chamber, with black anti-corrosion coating on the internal chamber wall.
With an observation window on the chamber door.
With an exhaust fan on the top of the chamber.
US original photometric system.
Easy to use operation software.
T14 EN 13501-1 Classification
Materials/products classified A1 according to EN 13501-1 of reaction to fire performance are considered to need no further testing:
All materials/products described in commission decision 96/603/EC (as amended);
Laminated glass where the internal organic layers are not exposed and the percentage mass of organic material is less than or equal to 6 %.
Materials/products classified A2 – s1, d0 according to EN 13501-1 are considered compliant with regard to flame spread, heat release, and smoke emission requirements only. The toxic emissions limit shall satisfy the requirements of R1 HL3 (CIT < 0.75).
EN 13501-1 Class A tests involved instruments:
Further introduction of EN 13501-1 Classification visit:
T15 Toxicity Gas Analysis for Wires & Cables
Compliance: EN 50305
Summary:
Measures the toxicity gases generated from 1 gram material combustion in 800°C tube furnace, analyzed gases content including CO2, CO, HCN, SO2, NOx.
Analysis Methods:
CO2 - NDIR CO2 Analyzer.
CO - NDIR CO Analyzer.
HCN - Spectrophotometry.
SO2 - Colorimetric Gas Detector Tube
NOx - Colorimetric Gas Detector Tube
The toxicity index (ITC) will be calculated to evaluate the performance.
Test Criteria:
The toxicity index, ITC.
Instruments involved:
Tube Furnace & Sampling Device.
NDIR Type CO/CO2 Analyzer.
Spectrophotometry, for HCN.
Colorimetric Gas Detector Tubes, for SO2, NOx.
T16 Glow Wire Test
Glow Wire Tester
Compliance: EN 60695-2-11
Summary:
Determine the flammability performance of electrical and electronic products by simulating the effects of thermal stresses produced by an electrically heated source to represent a fire hazard.
Test Criteria:
Minimum glow wire temperature, in °C.
MOTIS’s Glow Wire Tester:
Compact chamber with anti-corrosion black coating on the interior chamber wall.
Constant current heating device, temperature range of 500 to 1000°C.
Type K insulated thermocouple for temperature measurement, measuring range of up to 1100°C.
Hot wire application device, application force 0.95N, application depth 7mm.
Automated time record and hot wire application remove.
T17 Vertical Small Flame Test
Horizontal & Vertical Flame Chamber
Compliance: EN 60695-11-10
Summary:
Determine the flammability testing of plastic material used in electric devices and appliances by applying a 50w open flame.
Test Criteria:
Vertical small flame test classification.
MOTIS’s Horizontal & Vertical Flame Chamber:
Compact chamber with anti-corrosion black coating on the interior chamber wall.
Standard Bunsen burner, in accordance with ASTM D5207, can provide 50W open flame.
Flame calibration kit.
Sliding burner carriage for flame application.
Flexible sample fixturing, suitable for horizontal and vertical tests.
Motorized sample movement in the vertical direction.
Summary
EN 45545 is the mandatory European standard for materials used in the manufacture of railway vehicles.
All materials used in the manufacture of railway vehicles must follow the requirements of EN 45545 to protect passengers and staff by minimizing the possibility of fire and controlling the speed and extent of its development once it has occurred.
The EN 45545 contains 7 parts, where, EN 45545-2 specifies the detailed test requirements (Hazard Level) and test methods of materials according to their usage, characteristics, and vehicle categories.
Lastly, the material will be ranked as RxHLy based on the test requirements, and test methods.
Contents NAV
What is the EN 45545
How EN 45545 Created
45545 Purpose
EN 45545 Categories
EN 45545-2 Test Method
T01 Oxygen Index
T02 Lateral Flame Spread
T03 Heat Release Rate
T04 Horizontal Flame Spread of Floorings
T05 Single-Flame Source Test
T06 Calorimeter for seats
T07 Ignitability of Bedding Items
T08 Flash and Fire Points
T09.01 Flame Spread of Single Cables
T09.02/03/04 Flame Spread of Bunched Cables
T10 Smoke Density Test
T11 FTIR Gas Analysis
T12 Toxicity Test for Non-Listed Products
T13 EN 13501-1 Classification
T15 Toxicity Test for Cables
T16 Glow Wire Test
T17 Vertical Small Flame Test
Summary